Academy
IEC61508/ ISO26262: Designing Safety Critical Applications
A design toolbox for hardware, software and system Engineers. [WEB EDITION]
This course is intended for design engineers. It provides the fundamental ground of knowledge needed to enable R&D to operate in a safety critical design process and to interface with the Safety Managers.
When a product is recommended to meet any Safety related norm, professionals involved in the development of electronics hardware and software parts need to understand the foundation of Functional Safety and to adopt related processes and tools.
This training is structured as a general approach, to provide an extensive practical toolbox on how to effectively implement a safety-first design process. For this reason, It is focused on the fundamental elements of the IEC 61508 norm, which is the most extensive and general. ISO 26262 is also analyzed along with other important derived norms.
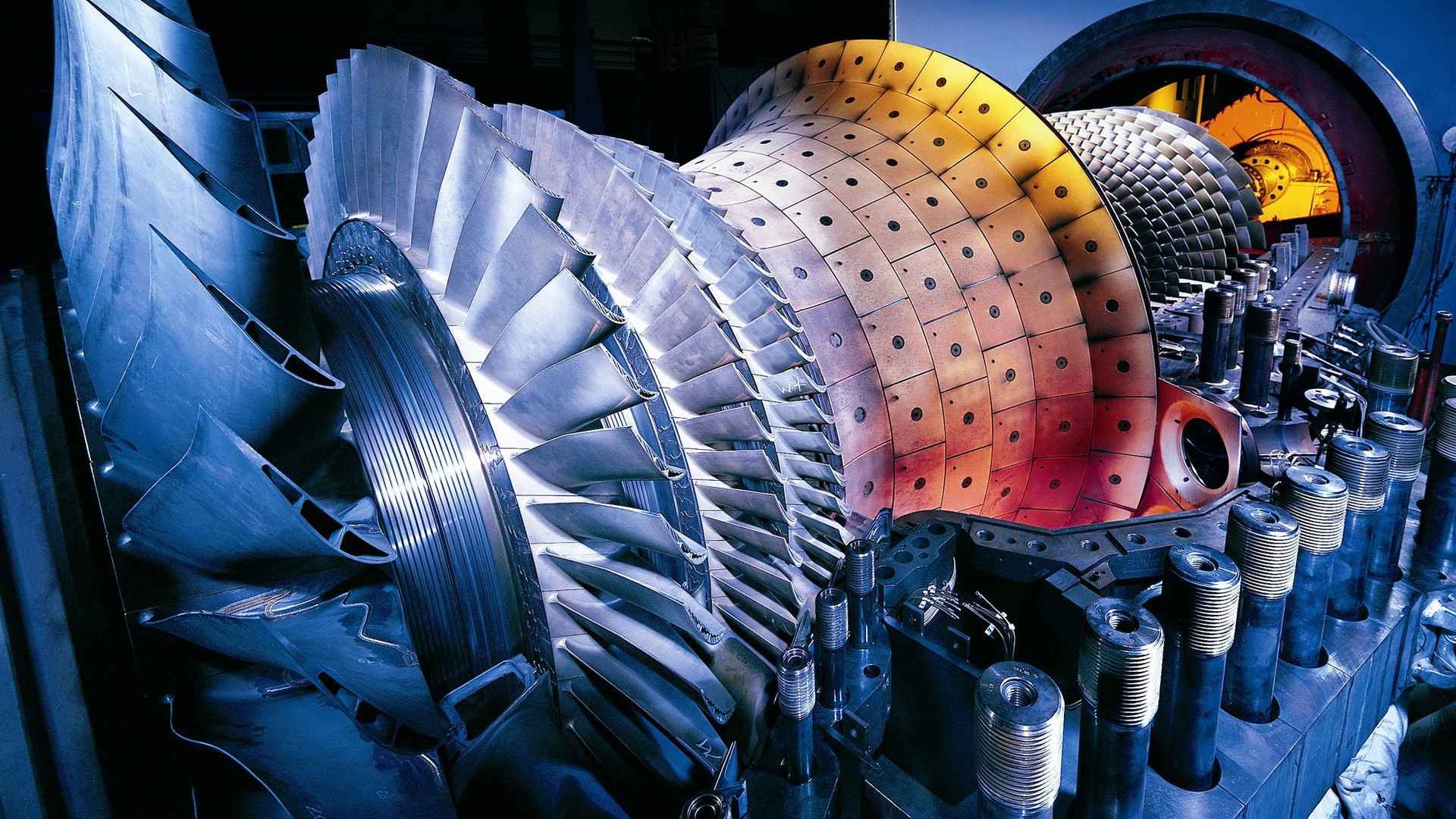
The training is organized into three lessons, web sessions of 4 hours, and some Q&A sessions with the expert.
– Lessons: (4 hour each) will be held by an experienced external trainer.
– Schedule: 8:30-13:00 with a break from 10:30-11:00
– Q&A: during the break time and before the end of the lessons will be possible to have a session of question directly with the expert
The webinar will be held on `zoom.us` platform, that is a free video conference application.
Session 1: Functional Safety fundamentals
- Functional Safety of E/E/PE
- history and basics
- random failures, systematic failures
- safety analysis methods
- proactive approach: functional safety lifecycle
- what’s SIL?
- an introduction to SIL norms
- what’s IEC 61508?
- base concepts contained in IEC 61508
Session 2: Implementation with example: system design and hardware
- Software integrity tools
- short introduction to norms derived from IEC 61508:
– automotive: ISO 26262
– industrial processes: IEC 61511
– railways and RAMS approach: EN 50126, 50128, 50129
– machinery: EN 62061, EN ISO 13849
- system design:
– Safety Plan and system features
– Hazard Analysis and safety functions features
– features allocation
- hardware design:
– general architecture
– architecture FMEA
– fault tolerance verification, fault detect coverage
– maximum resulting SIL with given hardware architecture
– detailed FMEDA, FTA calculation for max dangerous failure rate
– resulting SIL verification
Session 3: Implementation with example: software and system validation
- software design:
– features
– safety requisites
– safety integrity requisites
– architecture: software components and development tools
– planning: life cycle, documentation, resources, processes, methods, verification and validation techniques and plan
– development
– verification and validation
- final system validation