Application note
How to design Predictive Maintenance of Dynamic Systems using Artificial Intelligence
For industrial equipment, machinery and mechanical devices, product reliability is a major concern. In the last decades we witnessed the change of the maintenance techniques paradigm: from reactive to preventive at first, and from preventive to predictive at last
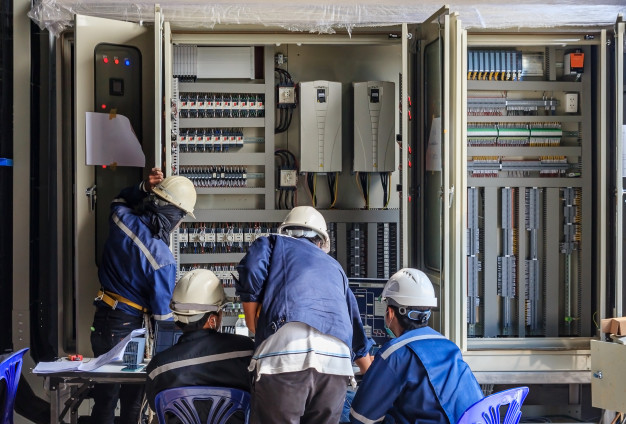
Overview
The answer comes from data mining techniques applied to the failure analysis and detection problem. The ML-machine learning algorithms allow for the estimation of the systems’ remaining useful life (RUL).
PdM is also called Condition Based Maintenance since RUL is estimated real-time on the basis of the involved condition indicators. These are physical parameters representing the health status of the system. Common application fields for PdM process are:
- electrical engines
- internal combustion engines
- industrial machinery
- medical devices
- consumer product with mechanical components (i.e. washing, cooling, cooking)
Read more to understand the possible routes for the development of a predictive maintenance application for embedded systems. The aim is to suggest a choice between possible approaches to the problem, and outline a road-map for the prototyping development phases.
Read more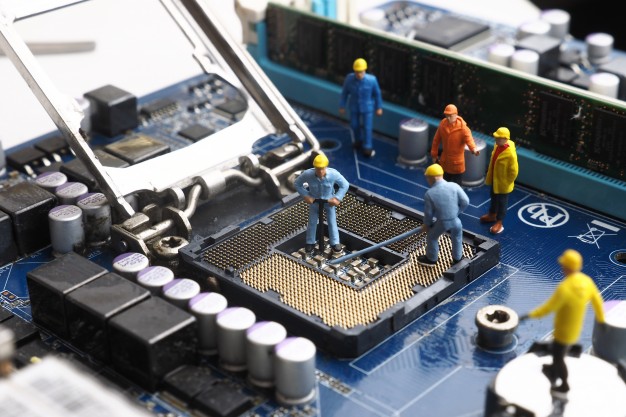
Fundamentals on Predictive Maintenance
For industrial equipment, machinery and mechanical devices, product reliability is a major concern. In the last decades we witnessed the change of the maintenance techniques’ paradigm: from reactive to preventive at first, and from preventive to predictive at last.
Reactive maintenance
Reactive maintenance (RM) acted after the system’s failure, leading to unsustainable downtime. Furthermore, acceptable reliability levels were granted by designing oversized products.
For instance, this paradigm is used today in the household appliances sector.
Preventive maintenance
Preventive maintenance (PvM) aims to keep the system’s health levels above critical thresholds by scheduling maintenance operations on a regular basis. These techniques avoid downtime operations, but at the same time lead to increased and sometimes unaffordable costs.
This paradigm is used in the car inspection and in the HVAC sectors, where maintenance is scheduled on a yearly or two-years basis.
Predictive maintenance
What if our product/system needs to:
- grant high reliability?
- act in an extremely competitive business?
In this case Predictive Maintenance (PdM) solutions add value to the product/system in terms of both reliability and costs.